Clear technical challenges are currently emerging in the machinery and mechanical engineering sector: the need for modernization, simplification, and standardization. At the same time, there is also a demand for extreme flexibility and agile processes, i.e. fast turnaround times combined with great ability to adapt to ever changing requirements. These opposing demands are often faced by engineering departments that already tend to be overworked, frequently resulting in conflicting goals during implementation.
The drive of the future
Drive technology is an essential driving force in all production setups, so when it comes to reconciling the technical conditions with the day-to-day reality of the production environment, it plays a central role. This means that it is also high time to find answers and solutions to allow the drive units to be adapted quickly, easily, and reliably. Erhardt+Leimer is tackling these challenges with its state-of-the-art drive concept EL.MOTION, which is setting new standards for Industry 4.0.
EL.MOTION for measurable optimizations
Der Antrieb für die Zukunft
Die Antriebstechnik als essenzielle Triebfeder jeder Produktion spielt bei der Vereinbarung der technischen Gegebenheiten mit der täglichen Produktionsrealität eine zentrale Rolle. Es ist daher höchste Zeit, Antworten und Lösungen für eine rasche, einfache und sichere Adaption der Antriebseinheiten zu finden. Erhardt+Leimer stellt sich mit seinem hochmodernen Antriebskonzept EL.MOTION dieser Herausforderung und setzt neue Maßstäbe für die Industrie 4.0.
EL.MOTION für messbare Optimierungen
EL.MOTION drive technology is used in a wide range of industrial applications. Precise alignment of paper webs in the printing industry, reliable transportation of goods, and the movement of mobile platforms are just a few of the areas in which EL.MOTION motors are used. Here is a selection of the potential industries where this drive technology can be used:
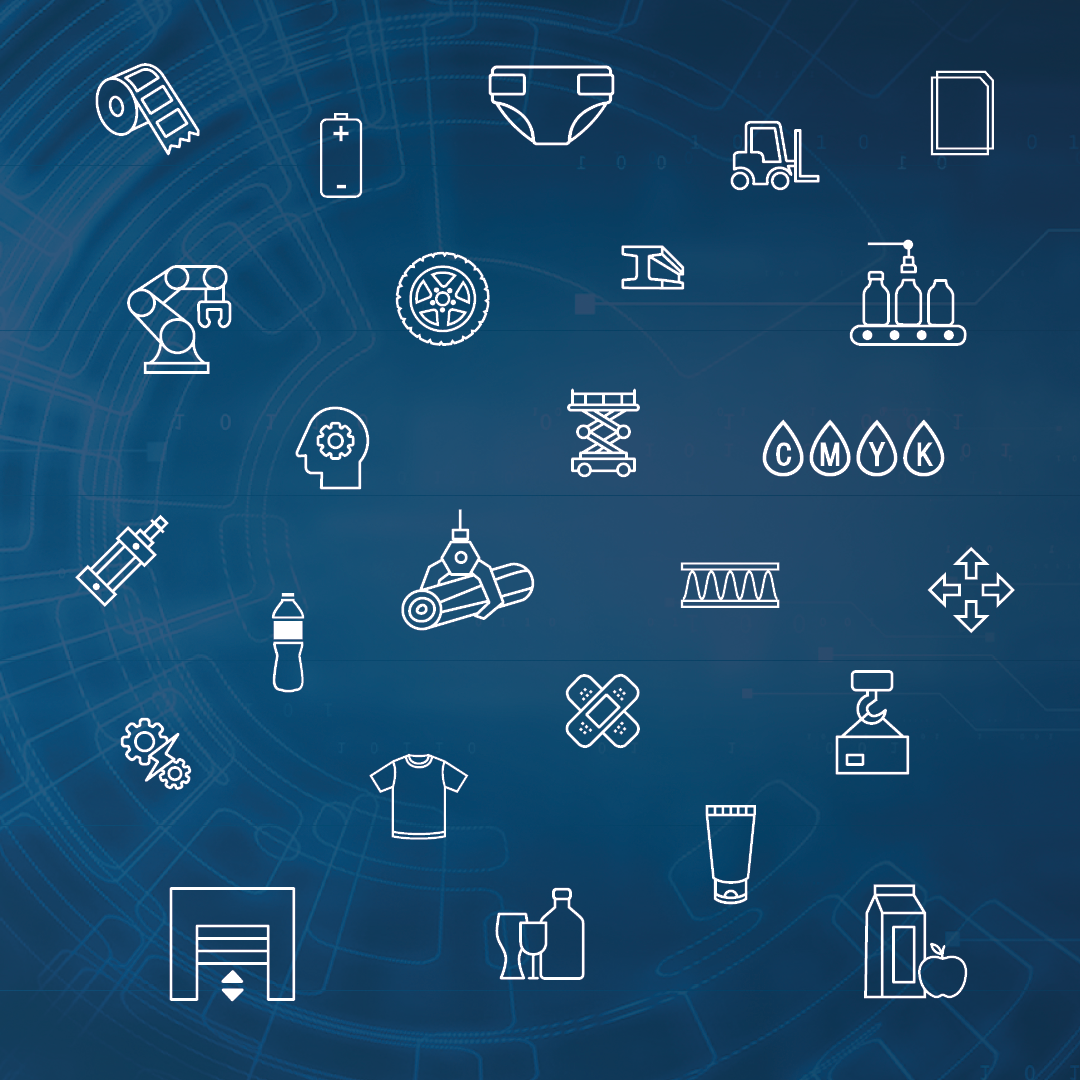
The EL.MOTION drive system includes a wide selection of gearless synchronous drives. The product portfolio contains linear and rotary BLDC motors as well as options for upgrades with gearboxes and safety brakes.
Linear drives
The linear drive units AG 72, AG 91, AG 93, and AG 96 are synchronous motors with high positional accuracy and control dynamics. They are particularly well suited to long-term applications and are used e.g. with moving webs for web control at unwinding and rewinding stations.
AG 72 | AG 91 | AG 93 | AG 96 | AG 98 | |
Nominal actuating force | 250 N | 1000 N | 3000 N | 5500 N | 10000 N |
Nominal actuating speed | 60 mm/s | 60 mm/s | 30 mm/s | 15 mm/s | 10 mm/s |
Nominal actuating travel | ± 6 to ± 50 mm | ± 25 to ± 100 mm | ± 50 to ± 200 mm | ± 50 to ± 200 mm | ± 50 to ± 300 mm |
Operating voltage | 24 V DC | 24 V DC | 24 V DC | 24 V DC | 24 V DC |
STO | Not available | Variant available | Variant available | Variant available | Variant available |
Link to AG 72 | Link to AG 91 | Link to AG 93 | Link to AG 96 | Link to AG 98 |
AG 72
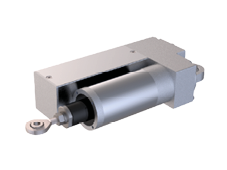
- 250 N
- 60 mm/s
- ± 6 to ± 50 mm
- 24 V DC
AG 91
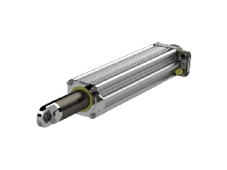
- 1000 N
- 60 mm/s
- ± 25 to ± 100 mm
- 24 V DC
- STO Variant available
AG 93

- 3000 N
- 30 mm/s
- ± 50 to ± 200 mm
- 24 V DC
- STO Variant available
AG 96
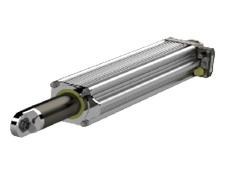
- 5500 N
- 15 mm/s
- ± 50 to ± 200 mm
- 24 V DC
- STO Variant available
Rotary drives
The rotary drive units AD 11, AD 12, and AD 14 are synchronous machines with a high power density. With stepless power adjustment, they can be used without a gearbox in many applications. High axial loads can also be handled without problems thanks to the additional support provided by a two-row angular ball bearing. As a result, the brushless drives can be connected directly – without a coupling – to a machine, which makes them very easy to integrate in existing production lines.
In addition, our rotary drives can also be supplied with optional upgrades such as brakes, planetary gearing, angular gears, or hollow-shaft gearboxes to ensure seamless integration in your application.
AD 11 | AD 12 | AD 14 | |
Nominal torque | 1.0 Nm | 2.4 Nm | 4.0 Nm |
Nominal speed | 1000 rpm | 350 rpm | 225 rpm |
Resolution, multiturn encoder | 12 bit/4096 | 12 bit/4096 | 12 bit/4096 |
Operating voltage | 24 V DC | 24 V DC | 24 V DC |
STO | Variant available | Variant available | In preparation |
Link to AD 11 | Link to AD 12 | Link to AD 14 |
AD 11
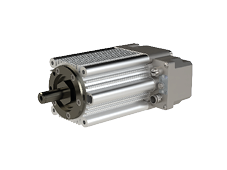
- 1,0 Nm
- 1000 rpm
- 12 bit/4096
- 24 V DC
- STO Variant available
AD 12
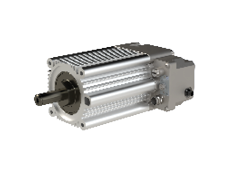
- 2,4 Nm
- 350 rpm
- 12 bit/4096
- 24 V DC
- STO Variant available
AD 14
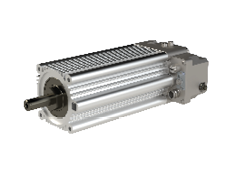
- 4,0 Nm
- 225 rpm
- 12 bit/4096
- 24 V DC
- STO in preparation
Our brochure contains everything you need to know about our range of EL.MOTION products, including all the technical details and software features a glance. We will also be very happy to assist you personally and help you to find the right motor for your application.
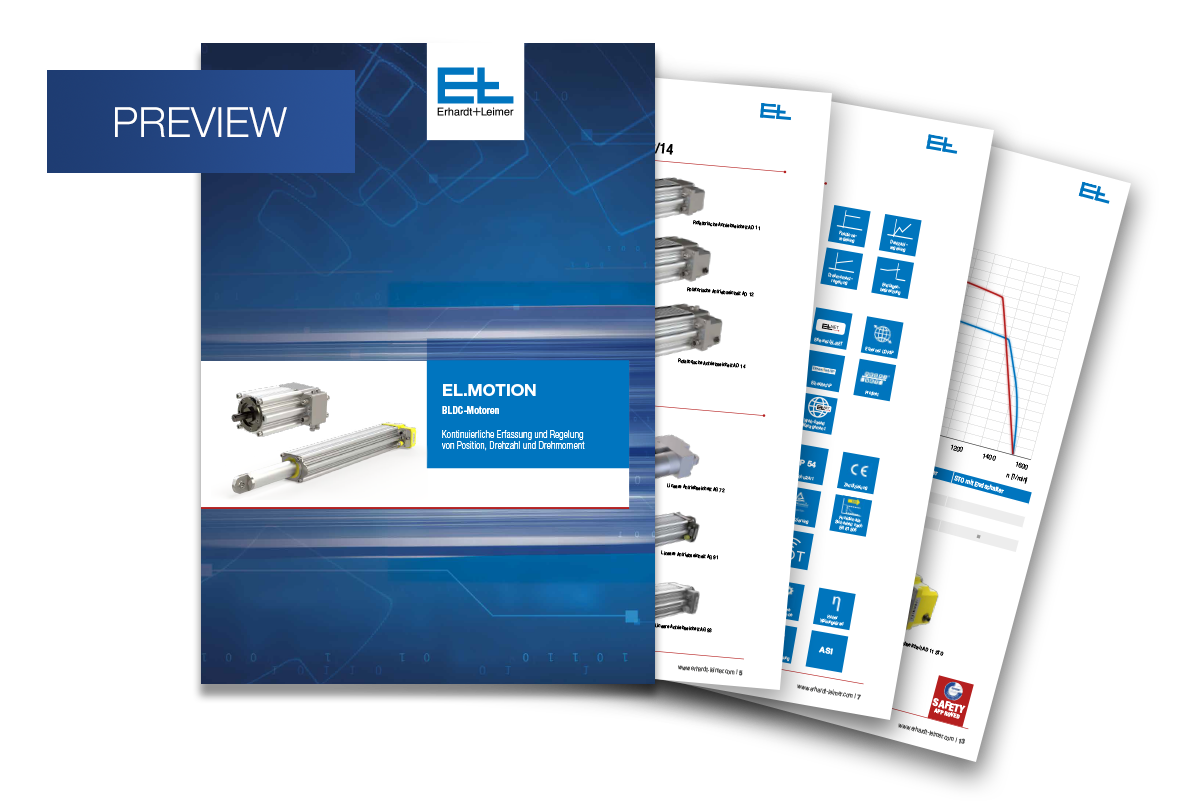
The EL.MOTION brochure contains the following:
![]() | Complete product portfolio at a glance Extensive insight into commissioning & software features Overview of all technical data & drawings |
Der EL.MOTION Prospekt umfasst folgende Inhalte:
![]() | Produktportfolio auf einen Blick Inbetriebnahme & Software Technische Daten & Zeichnungen |
Write to us! We are looking forward to your message.
"With EL.MOTION, Erhardt+Leimer has embarked into a new era of drive technology – one that will enable us to completely reshape our approach in a way that will benefit not only our existing customers, but also new customers from many different industries in equal measure.
Thanks to our own in-house development of drives, we have been able to round off the product portfolio of Erhardt+Leimer and – thanks to our know-how in the areas of web monitoring and web visualization, web guiding, and drive technology – we can now offer complete solutions to equip the production lines of our customers – all from a single supplier."
Andreas Heindl
Product Manager Drive Technology
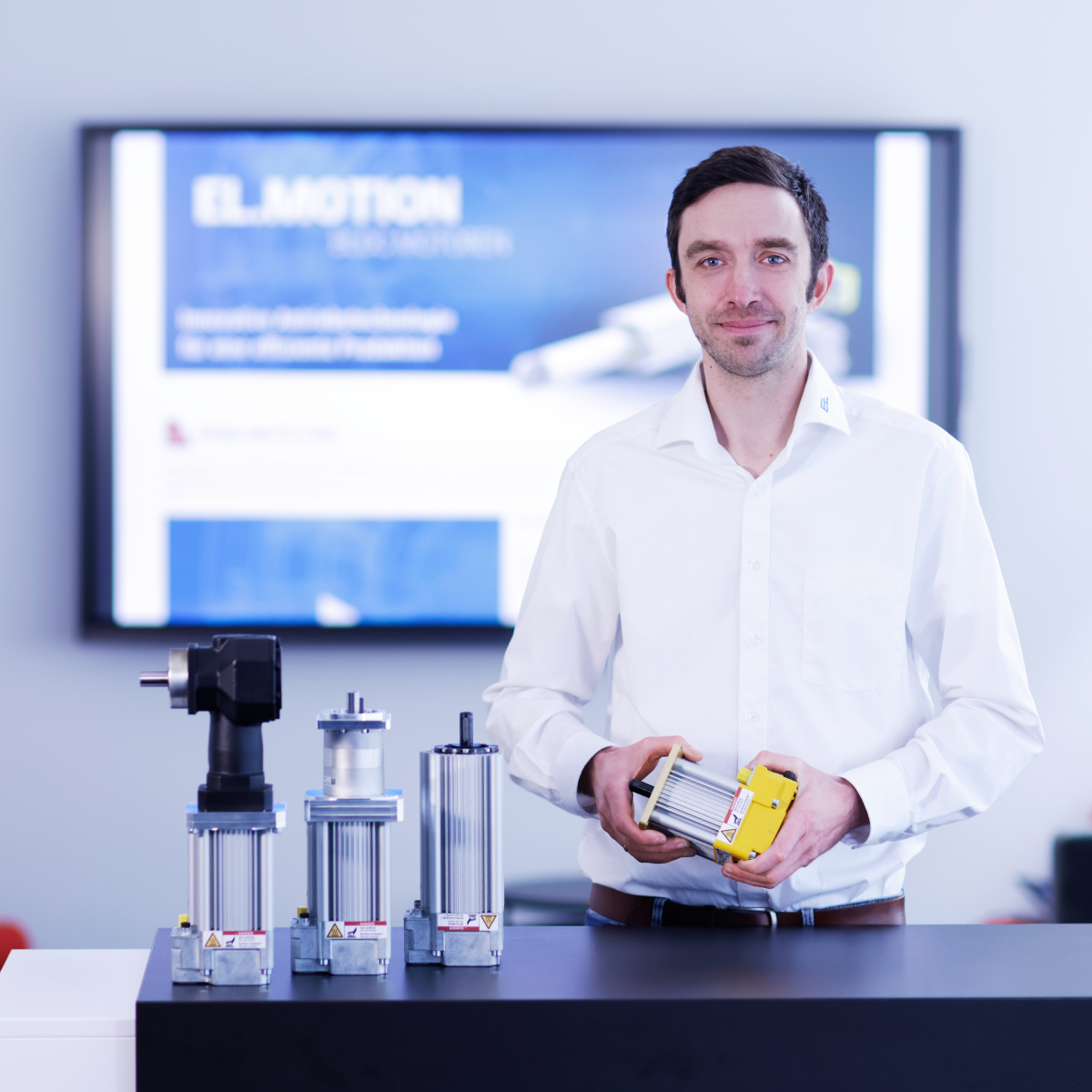
Operating principle and potential upgrades
Function
The pioneering innovation of EL.MOTION is that the previous BLDC machines in this performance class can now be replaced with synchronous machines. This opens up the ability to deliver the same highly dynamic performance and excellent control capability we are familiar with from gearless drives in a much smaller package. Despite the small form factor, fully integrated power electronics with a voltage failure-safe encoder system are already integrated in the system. The motors can be commissioned and taken into operation using any browser via the web-based management tool. With a standard integrated Ethernet interface that supports Ethernet UDP/IP, EtherNet/IP, and Profinet, all drives can be seamlessly integrated in existing production processes and are perfectly suited to Industry 4.0 concepts.
Area of use
The system can be used in industrial applications for position, speed, and torque control.
Application
The BLDC drives are designed for flange mounting. Different gearbox variants and an emergency stop brake are available as options.
Classic cascaded controller module comprising torque, speed, and position controllers. To ensure the highest possible efficiency, a vector control model with sinusoidal commutation is used. With the aid of an integrated multiturn encoder, the absolute rotor position can be transmitted via the communication data block to the customer's control system.
The majority of EL.MOTION actuating drives are also available as safe torque off (STO) variants. This safety feature, which is integrated in the drive and complies with EN 61800-5-2, switches off the motor torque by interrupting the control impulses.
Your advantages:
- The two-channel architecture (channel A and channel B) of the STO module achieves Category 3 and Performance Level d in accordance with EN ISO 13849-1.
- Safety for personnel and equipment
- Fast response times
- Web-based management is featured as standard on all drives.
- Enables settings and status queries via Ethernet in any standard web browser
- Open connectivity: access via EtherNet UDP/IP or via certified standard protocols such as EtherNet/IP, Profinet, and POWERLINK.
- Requires one IP address per drive in the network for integration
- Parameterizable – with intuitive commissioning via web-based management
- Comprehensive monitoring of all relevant parameters
- Guided, simple commissioning process and optimization of drive applications take a matter of seconds
- "One-click start" Automatic System Identification (ASI)
- Automatic adaptation of parameters to optimize them for the application
- Resonance detection keeps control settings at a safe distance from stability limits
- High stability and quality in motion control
We have a number of optional upgrades available for our rotary drives that will make it even easier to integrate them in your application:
- Planetary gearboxes
- Angular gearboxes
- Hollow shaft and solid shaft gearboxes
- Modular safety braking system