- Description
- Function drawing
Function
ELROLLER steering roller systems used for web guiding already correct the web position on the infeed plane. They consist of a fixed base frame and a movable guide frame. The latter accommodates one or two positioning rollers and swivels around an imaginary pivot point on the infeed plane. A steering roller is referred to as a proportional actuator, which means that it operates under friction and must not permit slipping between the web and positioning roller.
Area of use
ELROLLER systems are always used for web guiding where there is a long entry path due to technical process reasons.
Application
Depending on the available space, steering rollers can be equipped for web guiding with one positioning roller (web is guided with a 90° wrap) or two positioning rollers (lower wrap angles possible). The following applies when installing an ELROLLER for web guiding: The infeed path should be the equivalent of two to three times the web width, the outfeed path should be between 50 % and 100 % of the web width. The sensor should be positioned behind the positioning roller, as near to it as possible. This offers a short response time, creating improved actuating dynamics.
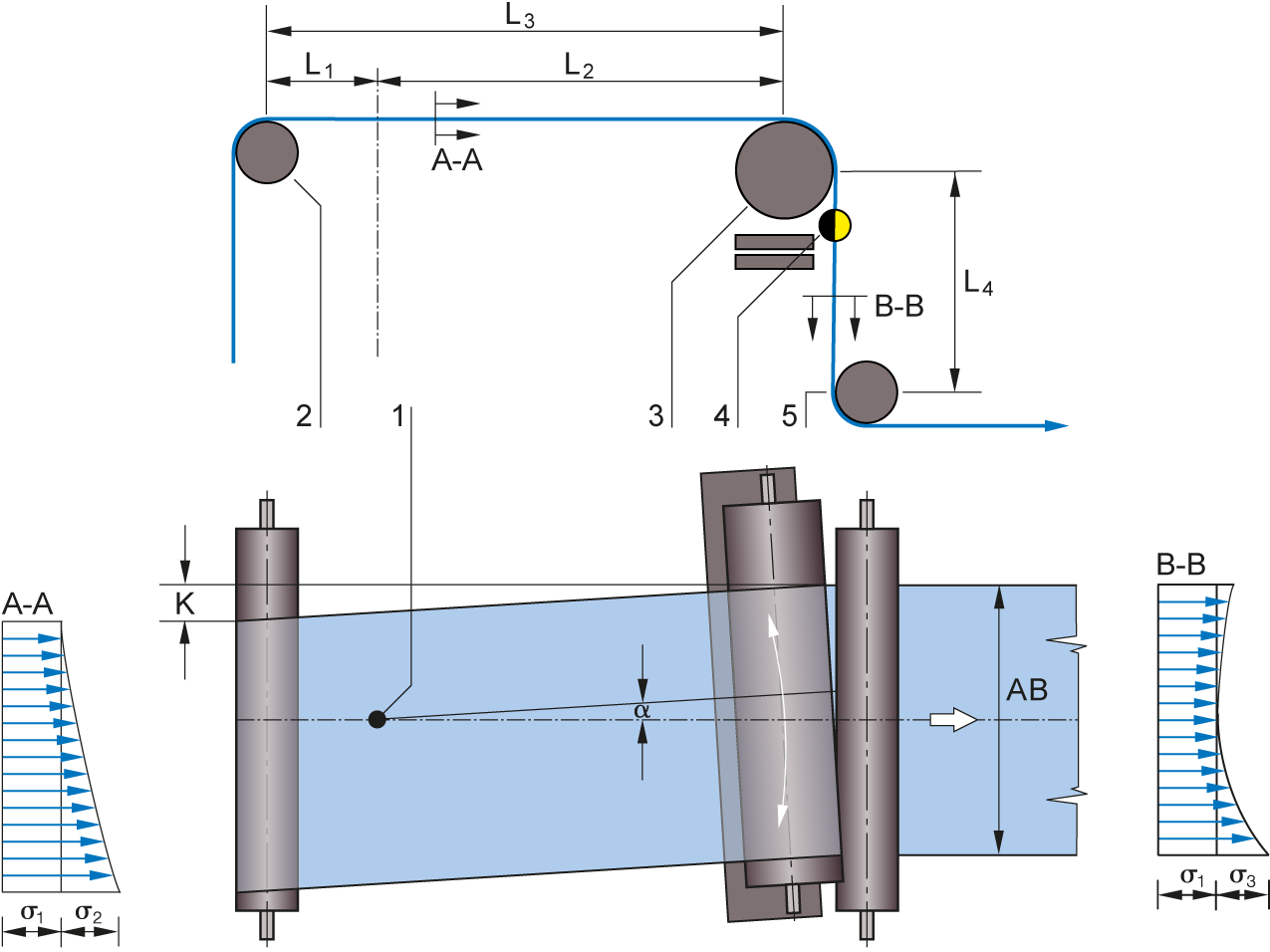
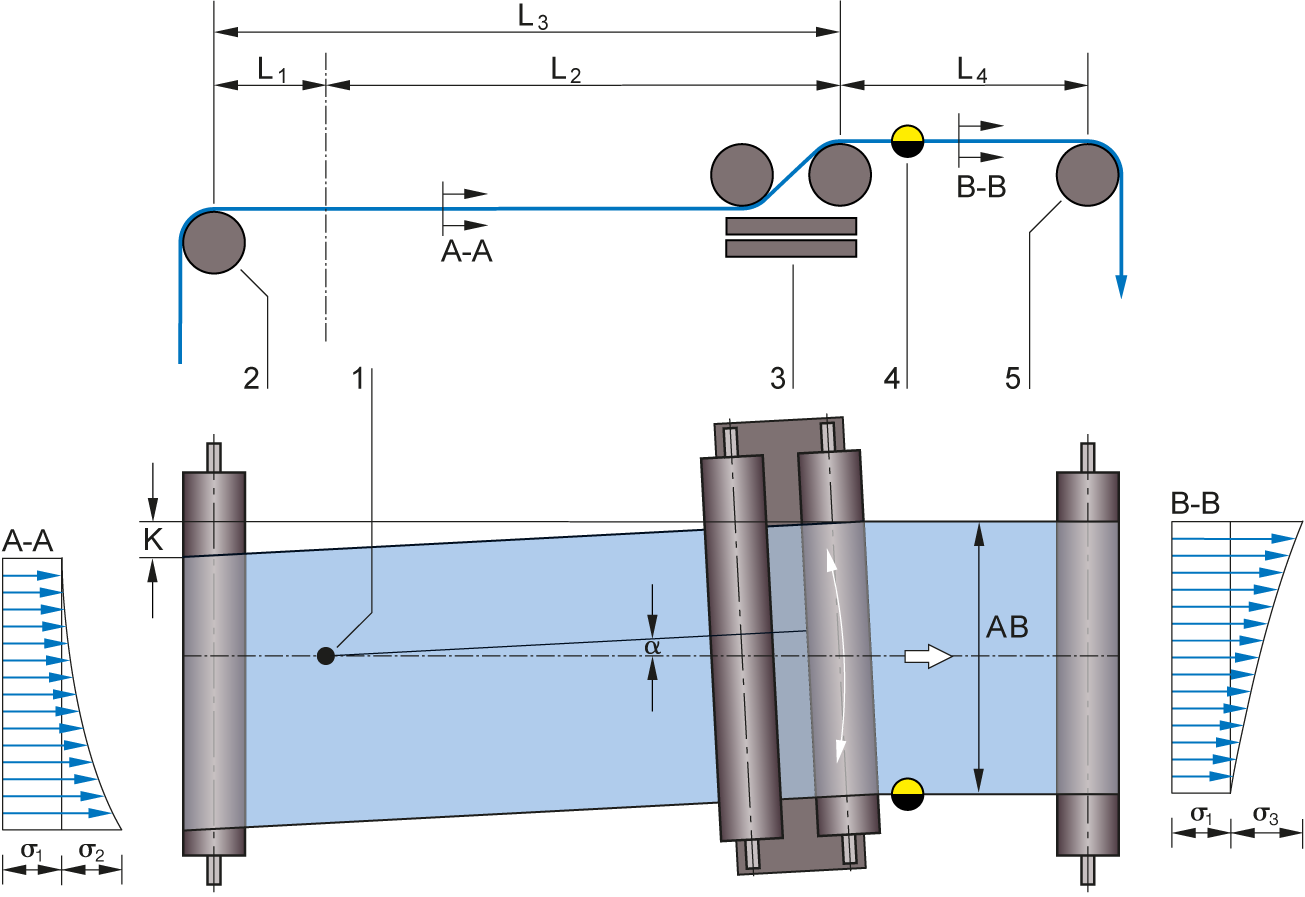
Legend
A = Web tension distribution at infeed | B = Web tension distribution at outfeed | K = Correction of the web guiding | a = Correction angle | σ1 = Basic web tension | σ2 = Tension distribution through swing movement of the roller frame at the infeed | σ3 = Tension distribution through swing movement of the roller frame at the outfeed | 1 = Pivot point | 2 = Infeed roller | 3 = Positioning roller(s) | 4 = Sensor | 5 = Fixing roller | L1 = Infeed path to the pivot point | L2 = Infeed path from the pivot point to the steering roller | L3 = Infeed path | L4 = Exit path